Drythane Roof Waterproofing Solutions
Comprehensive Protection, Durability & Sustainability—Optimised for the 2025 Monsoon
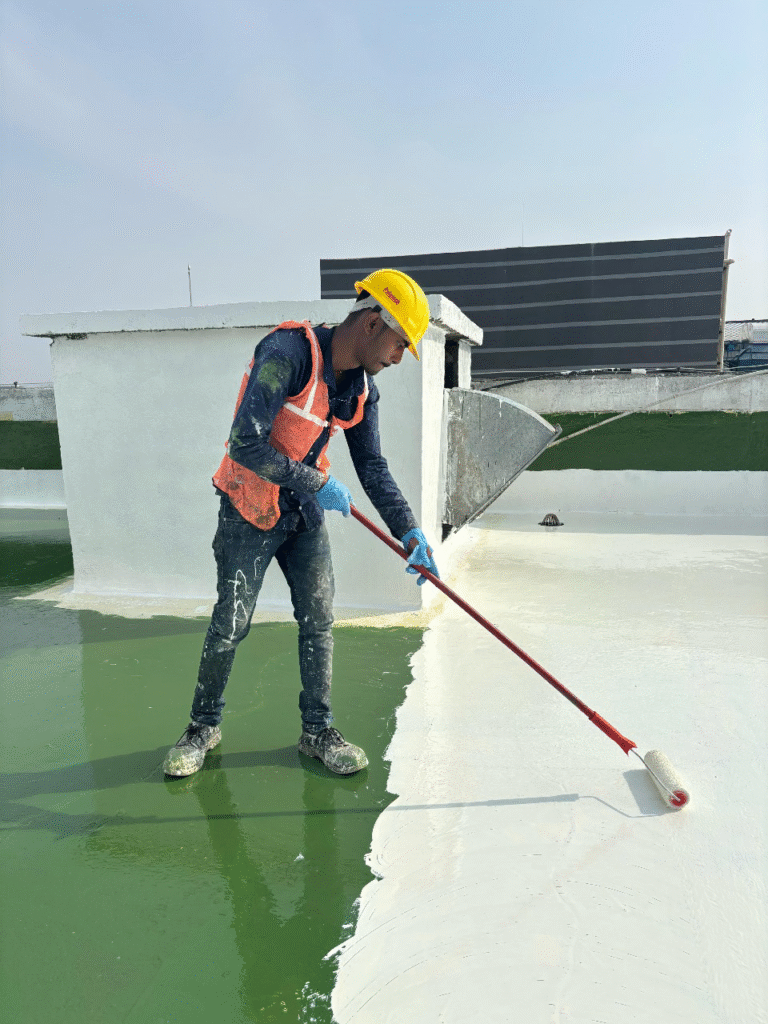
Drythane HE 400 – Hybrid Polyurethane / Polyurea
- Advanced chemistry: Polyurethane backbone married to hybrid polyurea for outstanding adhesion and elastic recovery.
- Performance envelope: Handles severe temperature swings, intense UV, and heavy precipitation without embrittlement or chalking.
- Lab-validated longevity: Accelerated-weathering and salt-fog tests confirm multi-decade service life.
Drythane Standard Combo System – Crack-Bridging Mastery
- Dual-layer design: High-build base + flexible hybrid top layer.
- Movement tolerance: Bridges live cracks ≥ 10 mm—no reinforcing fabric required.
- Versatility: Ideal for ageing slabs, expansion joints, and complex roof geometries.
- Full-lifecycle support: Certified applicators, detailed QA checklists, and scheduled maintenance inspections.
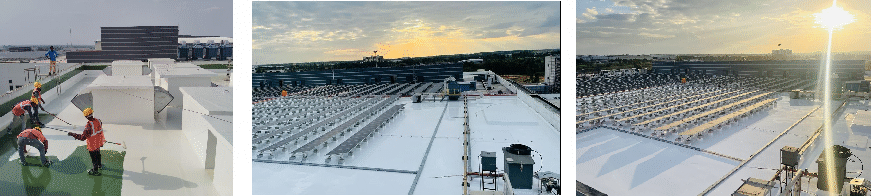
Aliphatic Cool-Roof Topcoat
- Solar reflectance: Drops roof-surface temperature by > 12 °C during peak summer, cutting HVAC load.
- UV armour: Aliphatic resin resists yellowing and chalking, preserving colour and gloss.
- Sustainability boost: Lower cooling demand translates to a reduced operational carbon footprint.
Spray-Applied Polyurea Systems
- Mechanical muscle: Tensile strength ≈ 25 N mm⁻²; elongation ≈ 750 %.
- Rapid return-to-service: Gel in < 10s; tack-free in minutes; trafficable within hours.
- Custom-built: Formulations tailored to chemical-resistant, abrasion-resistant, or potable-water applications.
Innovation & Sustainability
Continuous R&D investment, ISO-compliant QC labs, and collaboration with global coatings institutes.
Drythane
Web : www.drythane.com