The Evolution of Rebar Connectivity: Embracing Rebar Couplers
Accelerated construction growth demands quality connection, efficiency, and operability. Recent advance-ments in concrete design, new materials, and the development of composite structures have prompted designers to seek alternatives to lap splicing or welding for connecting reinforcing bars. Traditional methods of lap splicing and welding have proven inadequate for modern construction needs. Enter the rebar coupler, a solution offering better safety, sustainability, and cost reduction.
What are Rebar Couplers?
Joining rebars with couplers, known as mechanical splicing, involves connecting two reinforcing bars to behave like continuous lengths of rebar. Couplers, small steel connectors, provide total tension capacity. The commonly used threaded system, with its simple yet brilliant design, reduces the amount of reinforcement required.
Benefits of Using Rebar Couplers
Reducing Rebar Congestion
Traditionally, lapping reinforcements were necessary in concrete buildings to ease rebar transportation and handling. However, this method can lead to heavy reinforcement congestion in concrete members, complicating concrete placement and potentially affecting structural integrity. Rebar couplers eliminate this problem by maintaining a manageable steel-to-concrete ratio, facilitating the concrete placement process.
Independence from Surrounding Concrete
The load transfer in lap joints depends heavily on the bonding of the surroun-ding concrete. Poor compaction or degradation can significantly affect the performance of the splice. When two reinforcing bars behave as a continuous unit through the use of rebar couplers, reliance on concrete for load transfer is eliminated, promoting full strength in tension.
Preventing Damage to Formwork
Preparing starter bars that project through the formwork has traditionally presented challenges such as safety hazards from protruding bars and the need for perfectly predrilled holes in timber formwork. Rebar couplers eliminate these challenges by providing a straightforward method for connecting starter bars.
Cost Savings
Rebar couplers contribute to significant cost savings in construction projects by reducing the amount of steel used, resulting in up to 40% savings on rebar costs. Additionally, rebar couplers decrease construction time and the amount of reinforcing steel needed. Other cost-saving benefits include:
- Reduction of material waste from overlap splices
- Cost-efficiency in overall project costs, especially with larger rebar sizes
- Savings on rebar and freight costs
- Mitigation of job site problems due to rebar congestion
- Prevention of damage to costly forms, rendering them reusable
- Reduction of labour, designer, and detailer costs
- Minimisation of project delays due to installation inefficiency
Contributing to Sustainability Goals
Reinforced concrete structures consume enormous amounts of concrete and rebar during construction. Rebar contributes the most CO2 per unit weight compared to other resources, contributing approxi-mately 9.2 times more embodied CO2 (ECO2) than concrete. Mechanical rebar couplers significantly reduce ECO2 emissions by over 80% compared to splice lap. By using couplers to connect rebars, construction projects can build greener and lighter buildings, optimising rebar work and achieving sustainability goals.
Common Types of Rebar Couplers in India
Various coupler systems are available for different applications. Leviat, a CRH company, features industry-trusted brands like Moment. Our renowned Moment JoinTec (JT) Coupler ensures a full-performance splicing joint with its proof-stressed bar ends. The extended long thread provides swift installation by simply turning the coupler instead of the bar. Its parallel thread assures positive alignment, locking the connection and maintaining continuity and structural integrity.
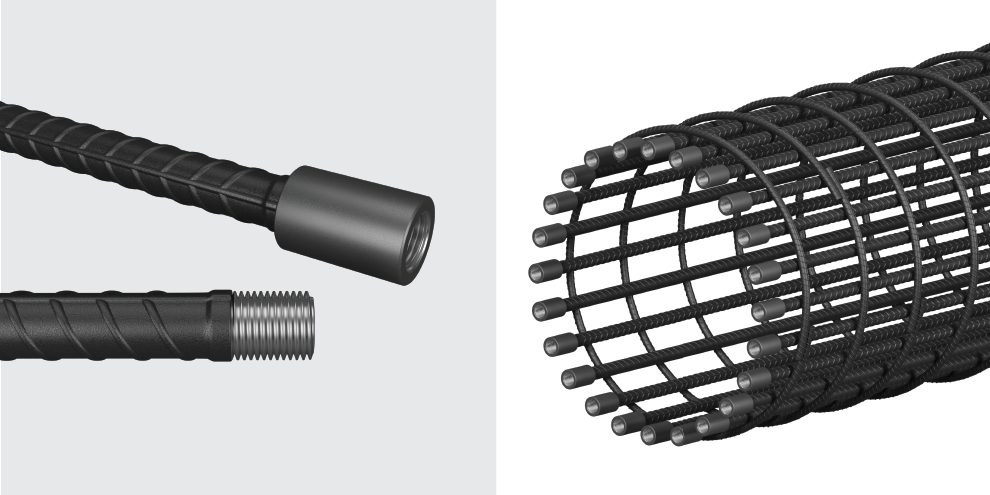
The Moment Grout Coupler, uniquely designed for precast concrete connec-tions, offers high flexibility and tolerance. When coupled with the Moment JT threaded system and Moment’s proprietary 100MPa grout, it can carry high loads exceeding the strength of the rebar.

Conclusion
The advancement of steel thread coupler technology has enabled rebar couplers to revolutionise the construction industry by providing quality connectivity, efficiency, and operability. Rebar couplers eliminate the inefficiencies and challenges associated with traditional lap splicing and welding methods. They reduce rebar congestion, prevent damage to formwork, and significantly lower construction costs. Furthermore, rebar couplers contribute to sustainability by reducing ECO2 emissions. As construction demands continue to grow, rebar couplers offer a modern, efficient solution that meets the needs of today’s construction methods while promoting eco-friendly practices.
Leviat India Pvt. Ltd.
Web : www.leviat.com/en-in