CLOOS – Stay one step ahead of the latest trends and challenges in welding technology and find out how to meet them with innovative solutions from CLOOS!
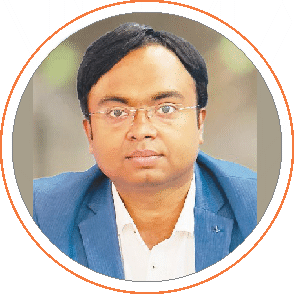
Cloos India Welding Technology Pvt. Ltd.
Trend 1: Growing Automation
The rise of automation continues to reshape welding processes, enhancing efficiency and precision. At CLOOS, we use advanced technologies to integrate robotic welding solutions seamlessly. Our all-in-one approach ensures easy integration and no gaps between proce-sses, keeping your welding operations with the demands of the modern era.
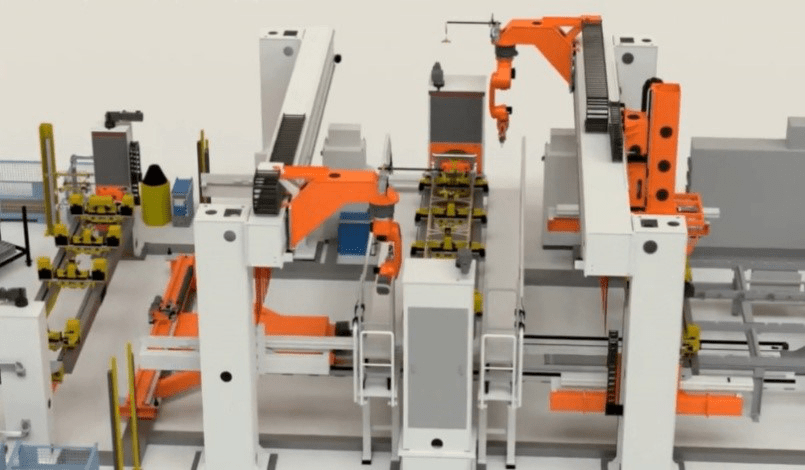
Trend 2: Sustainable Welding Practices
In 2025, the welding industry will switch to sustainable methods. CLOOS offers environmentally friendly solutions such as welding fume extraction to minimize environmental impact, protect employees, and optimize energy consumption. Let’s create a sustainable future through responsible welding.
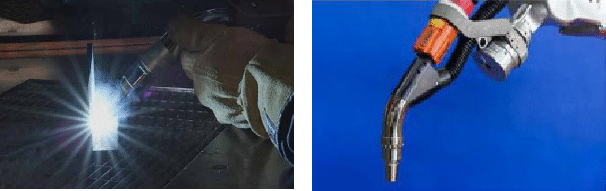
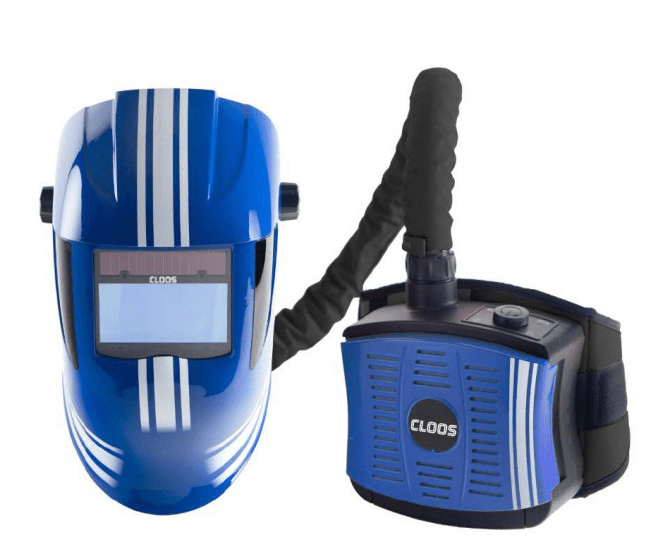
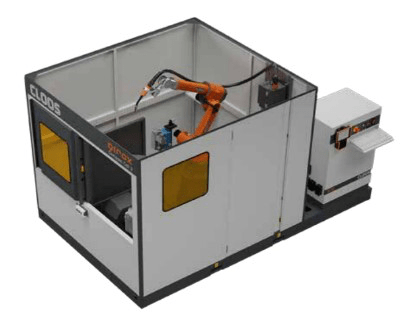
Trend 3: Skilled Workforce Shortage-
The shortage of qualified welders remains a challenge, but CLOOS is closing the gap. Our QINEO ArcBoT and our compact robot cells make welding accessible to a wider range of operators. This ensures that welding is preserved while a new generation of welders can be trained.
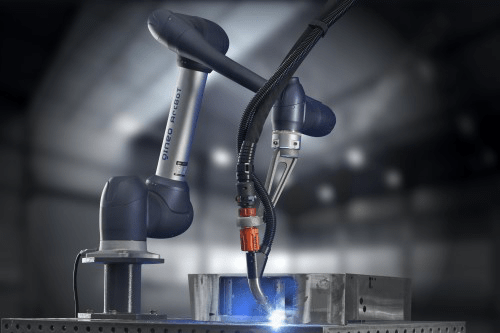
Trend 4:- Optimized welding preparation CLOOS Arc Sensor simultaneous measuring and welding to ensure sustainability & Quality without laser CLOOS arc sensor enables measurement and welding to occur simultaneously with minimal loss in time. The welding torch oscillates along the edges of the weld seam, measuring for differing values on either side. The computer-based robot controller then adjusts the welding head position to place the seam exactly in the center of the joint and corrects the distance of the welding torch to the workpiece if the measured values are not the same on both sides. At the same time, workpiece distortions are corrected for without need for additional parts.
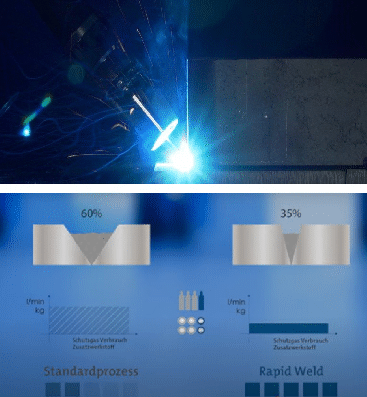
Trend 5:- Reduce cost by energy savings and less post weld work by innovative welding process:- Since 1919, Carl Cloos Schweisstechnik GmbH has been one of the leading companies in welding technology. CLOOS developed almost greater than 15 nos. welding technology. out of those, if we discussed about only two innovative welding processes (Rapid Weld and Speed weld) significantly reduce the use of filler material and shielded gas due to very small opening angle with high welding speeds because of the highly powerful arc. You benefit from the excellent weld quality due to the deep penetration. You avoid extensive reworks as spatters and undercuts are reduced to a minimum.. You reduce the welding time as considerably less welding layers are necessary.
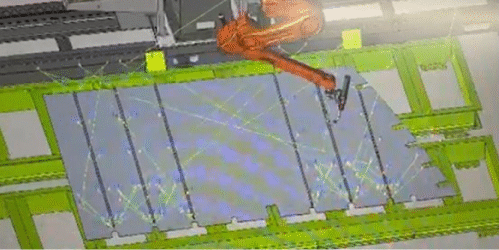
Trend 6: Digitalized Production-
The digital revolution is in full swing, and welding is no exception. Monitoring and controlling production in real-time is of paramount importance. With CLOOS C Gate, all digital solutions are in one place so that you can check production data effortlessly.
CLOOS RoboPlan – Revolutionizing Robotic Welding Programming
As the demand for precision, efficiency, and customization grows in industrial automation, CLOOS stands at the forefront with its innovative RoboPlan software – a cutting-edge offline programming and simulation solution for robotic welding.
Cloos India Welding Technology P. Ltd.
Email : contact@cloos.in
Web : www.cloos.de