Concrete is the most used material for construction, and its composi-tion plays a critical role in deciding the structural performance as well as carbon footprints and sustainability of structures in which it is used. In this short review, we will try to focus on few areas which may have an impact on overall performance of the concrete structures.
Concrete composition
The composition of normal concrete is fixed by using standard mix designing practices. Although the practices are consistent, the composition of concrete may still have variations based on factors like ingredient availability, quality as well and specification requirements. For high-performance and special concretes, mix design techniques are quite complex. Due to its performance requirements and sensitivity to variations, quality control at the production place and placement site plays a key role in its success.
Traditional mixes are mainly a mixture of cement, fine and coarse aggregates, water, and chemical admixtures. However, due to sustainability, cost, and availability concerns, the use of SCMs as well as recycled aggregates has gained acceptance. Types of cement have also been modified using fly ash, slag, and lime additions. Apart from the main objective of consuming industrial by-products, SCMs also provide some added benefits such as reduced water permeability, higher long-term strengths, and sulphate resistance to name a few. The use of SCMs also results in reduced carbon footprints of the structure.
Due to the unavailability of river sand, the industry in many parts of India and the world has shifted towards manufactured sand and some recycled alternatives. All these changes have also created challenges in maintaining concrete quality. This coupled with input cost increases and market competition has put the concrete producers on a tightrope.
Due to continuous changes in raw material properties and composition, it sometimes becomes difficult to understand the reasons for concrete quality variations. For example, early slump loss or on the opposite side setting delays can be attributed to cement or admixture performance but presence of clay or silt in sand as well as variation from SCMs may also produce the same deviations. Further adding to the complexity, it is known that different brands of cement offer different performance. The pace at which the RMC industry operates, such issues often hamper productivity and result in cost escalations.
Variations in concrete quality affect the placement, and finishing and may also have an impact on structural perfor-mance. For example, if bleeding can not be controlled, it delays the finishing work and also results in various cracks like plastic shrinkage, plastic settlement, and early-age drying shrinkage. In case of early slump loss, depending on the reasons, it may adversely affect the placement, compaction, finishing as well as compressive strength. Cracking may further lead to durability issues and would need repairs.
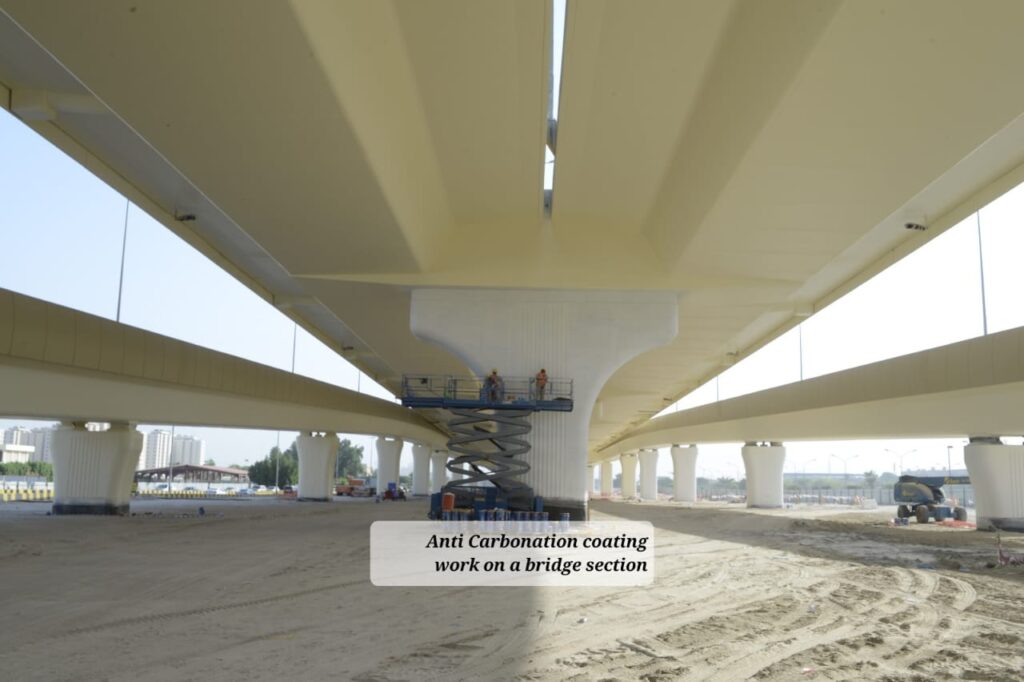
Water is an important part of the concrete composition. It’s required for hydration as well as some plastic properties. Maintaining w/b ratio and controlling on-site and in-transit additions can pose a major challenge. Deploying technologies such as w/b ratio probes and sensors which can help monitor the w/b ratio in transit is one of the most effective technologies. Particularly, special concretes such as pervious mixes or UHPC are very sensitive to water content variations. Rheology of UHPC is critical and it may be necessary to monitor the rheology on a real-time basis during transit and placement using concrete or grout rheometers.
Environmental aspects have driven the market towards more sustainable materials which has helped innovative technologies such as geopolymer concrete to enter the non-structural and repair segment. Quality control of geopolymer-based mixes is very different from normal concrete as its performance depends on the alkali activators as well as pozzolanic materials. Improperly designed mixes may result in lower performance and excessive alkali leach out.
Construction Practices
Apart from the composition, the quality of concrete depends on mix design efficiency, quality of ingredients, mixing, and transportation. The quality of fresh concrete directly affects the placement and finishing activities. Once the concrete is delivered to the site and is within the acceptable quality norms, then the quality and performance of the hardened concrete mainly depends on construction practices.
How efficiently the concrete is placed, compaction techniques, leveling and finishing of slabs, curing, and de-shuttering are the main activities that decide the final properties and performance of the hardened concrete elements. In case of precast concrete, handling and transportation of elements and various activities such as pre-tensioning are also critical.
Structural performance
The performance of structures depends on the quality of materials used in construction. There are various performance parameters such as load carrying capacity / compressive strength, cracking resistance, flexural strength, abrasion resistance, water and chloride permeability etc. All these parameters can be controlled by ensuring the quality of concrete.
Deviating from the quality requirements can lead to severe performance issues. In worst cases, these issues may result in structural stability risks. In most cases although, it necessitates repairs and strengthening work which will delay the projects and escalate costs. Overall, it may affect the service life and increase the lifetime repair and maintenance costs.
Quality issues also affect various finishing activities such as waterproofing, tiling, sealing, and coating. For example, improperly constructed retaining walls or roof slabs generally necessitate crack injection and other repairs. Such additional activities mean delays and increased costs. Issues with achieving target compressive strengths also result in repairs or retrofitting needs and sometimes demolition.
Considering the structural performance, costs, and timeline constraints, it’s important to control quality at each stage. Some new technological tools are available for monitoring quality of placed or hardened concrete such as maturity sensors, resistance measurements etc. These are non-destructive in nature and provide useful information on a real-time basis.
Training the manpower, observing good industry practices, monitoring quality, and using statistical analysis are a few measures that may help.
Protection of Concrete Structures
For good quality concrete, the requirement of protection, repair as well as maintenance is much less than average or poor quality concrete. The protection of concrete is essential as the concrete is exposed to the environment. Depending on the type of environment, concrete structures may have to withstand chemical and physical exposure. Chemical exposure may be chlorides, sulphates, carbon dioxide and other air pollutants or it may also be industrial chemicals and sewage. Most concrete structures are exposed to water either from natural sources or from domestic and industrial uses.
Physical exposure could be in the form of temperature gradient, vibrations, load, movements, shrinkage, settlement, abrasion, etc.
Concrete has some inherent porosity and cracks due to shrinkage at various stages. It can not be placed in one pour and due to which there are various types of joints which include construction joints, control joints and expansion joints.
In order to minimize the impact of physical and chemical exposure, it’s essential to use proper protective treatments over the concrete surface, joints, and connections. The protective treatments include waterproofing, joint sealing, crack repairs, protective coatings, and anti-carbonation coatings. It also includes various measures for controlling corrosion such as sacrificial anodes, ICCP, use of corrosion-inhibiting admixtures, and anti-corrosive coatings.
All buildings and infrastructure require waterproofing and drainage systems. Modern buildings, whether residential or commercial mostly have basements. As the basements are surrounded by retaining walls or diaphragm walls, the waterproofing generally starts even before the retaining walls are poured. Quality of construction plays an impor-tant role in ensuring the effectiveness of waterproofing systems. If the walls have deformities such as honeycombing, cracks and joint failures, it might lead to premature failure of the waterproofing systems. Various water bodies as well as softscapes are also important features of modern buildings. Podiums, terraces, and balconies either face the rain or are exposed to water from internal sources. Porous or cracked concrete would need a lot of preparation before the main waterproofing system is applied.
Concrete is alkaline and it needs to remain in alkaline state throughout its life cycle. Carbon dioxide in the air reacts with lime in concrete and may reduce the pH of concrete. This results in loss of passivity of the steel reinforcements inducing corrosion. To avoid carbonation, most infrastructure, particularly bridges exposed to heavy vehicular traffic are coated with anti-carbonation coatings.
Ingress of chlorides also causes corrosion. Care is generally taken while developing concrete mixes which are exposed to chloride environments. This means that they need to have very low chloride ion permeability. Corrosion-inhibiting admix-tures are also used in certain extreme exposure conditions. If concrete in such environments develops cracks, it becomes essential to evaluate the root cause on priority and if it’s not due to corrosion or ASR, then the cracks must be sealed to avoid ingress.
Expansion joints are provided for accommodating either thermal, seismic, or other movements. These joints need to be properly sealed while keeping the joint movement as per design requirements. Using rigid materials or partial closure of joints may lead to serious structural issues and cracking. There are many options including liquid sealants, joint tapes, and preformed seals. Proper handling and monitoring of the expansion joints will enhance the overall health of the structures and reduce maintenance/ repair needs.
These are only a few examples. Every structure may have unique waterproofing and protection requirements and a proper analysis and design would add value.
Summary
Indian construction industry is growing at a very fast pace and is also evolving continuously to meet the ever-increasing market expectations to maintain and improve the quality. The quality of concrete should be monitored, controlled, and improved to ensure the performance of structures and overall sustainability. Apart from this, it’s also essential to provide adequate protection to the structure for taking care of exposure and usage conditions. Training, adopting new technology, and staying updated on new trends and specifications will enable the industry to meet its targets and avoid escalation of costs and timelines.
Mr. Deepak Kanitkar – Director
Anudeep Constructive Solutions P. Ltd.
Web : www.constructionsol.com