
The construction industry, together with the materials industries which support it, is one of the major global exploiters of natural resources, both physical and ecological. The industry thus contributes very significantly to the current unsustainable development path of the global economy as it attempts to identify the principal ways in which construction contributes to environmental stress, and to quantify the contribution of construction where possible. Cement substitutes are materials that may be substituted, to some degree, for cement in order to improve different properties, such as strength and longevity. The use of cement substitutes is generally encouraged because of the environ-mental advantages gained from their diversion from the waste stream, the reduction of the energy required in their re-purposing (as compared to the manufacture of cement), and the conservation of raw materials, such as silica, alumina and iron oxide. The production of Portland cement is not only costly and energy intensive, but it also produces large amounts of carbon emissions. The production of one ton of Portland cement produces approximately one ton of CO2 in the atmosphere.

The global production of cement has grown very rapidly in recent years, and after fossil fuels and land-use change, it is the third-largest source of anthropogenic emissions of carbon dioxide. The global cement industry contributes around 6% of all man-made CO2 emissions and is consequently responsible for around 4% of man-made global warming. CO2 emissions trading is likely to be of huge importance to the industry in the future. Therefore, alternative cementitious materials are going to be in focus for industry.
Keywords: Portland slag cement, Sustainability, GGBS

Advantage of Alternative cementitious materials
Alternative cementitious materials are finely divided materials that replace or supplement the use of Portland cement. Their use reduces the cost and/or improves one or more technical properties of concrete. These materials include ground granulated blast furnace slag(GGBS), condensed silica fume, limestone dust, cement kiln dust, and natural or manufactured pozzolans like Flyash.
The use of these cementitious materials in blended cements offers advantages such as increased cement plant capacity, reduced fuel consumption, lower greenhouse gas emissions, control of alkali-silica reactivity, or improved durability. These advantages vary with the type of alternative cementitious material.
Green Materials as alternatives
Ground Granulated Blast-furnace Slag (GGBS) & Portland slag cement (PSC)
GGBS is a by-product of the iron and steel industry. In the blast furnace, slag floats to the top of the iron and removed. GGBS is produced through quenching the molten slag in water and then grinding it into a fine powder. Chemically it is similar to, but less reactive than, Portland cement (Pc).
When mixed with water it will hydrate in a similar way to Portland cement. It is always used in combination with Portland cement, typically in the range GGBS-30-70% Replacement of Portland cement.
Concrete made with GGBS cement sets more slowly in very initial days, than concrete made with ordinary Portland cement, depending on the amount of GGBS in the cement mix, but also continues to gain strength over a longer period leading to improved overall durability and life expectancy.
Portland Slag cement is manufactured by either inter- grinding the Portland cement clinker, Gypsum and granulated slag or blending the ground granulated blast furnace slag (GGBS) with Ordinary Portland cement by means of mechanical blenders.
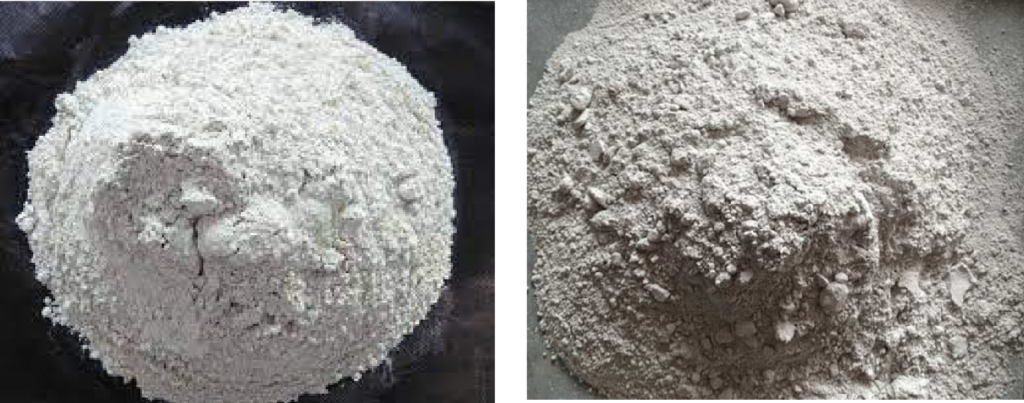
Superiority of Concrete with Cementitious Materials
- Increases the later age strengths by- 25 – 40%
- Reduces the heat of hydration by -35%
- Reduced pore volume in concrete by -60%
- Increased water tightness in concrete by -34%
- Resistance to Sulphate attack in concrete by -60%
- Resistance to Chloride attack in concrete by -90%
- Resistance to Alkali-Aggregate reaction in concrete by – 86%
Application of GGBS & PSC
- RCC in all types of foundations and super structure works.
- General building construction.
- Express ways, Roads and Metros.
- Mass concrete works in Dams, Spillways, Canals, Foundations etc
- Under ground works, Retaining walls, culverts and drainage works
- Effluent and sewage treatment plants
- Grouts and Mortars and Cement based products
- Waterproofing, Plastering, brick work and finishing works
- Marine works

Conclusions:
- The use of GGBS & Portland Slag cement (PSC) is well established in Concrete, Infrastructure & precast Industries.
- The past several years , there has seen a substantial growth in the use of PSC all over the world since it offers superior concrete properties.
- Use of PSC and GGBS leads to Pore refinement and grain refinement due to the secondary hydrated mineralogy, thus contributing for impermeability and enrichment of transition zones.
- Improved impermeability of the concreting resulting increased resistance against the ingress of moisture and gasses.
- PSC Improves workability, better compatibility with admixtures.
- Low C3A cement (SRC) was not recommended In marine environment, As C3A is important to trap chloride ions entering the concrete.
- Similar recommendations exist in IS 456 in case chloride is encountered along with Sulphate in soil or ground water, Portland Slag cement with more than 50% GGBS is recommended in place of SRC.
- Use of PSC in concrete is recognized by LEED etc. and add points towards LEED certification.
- The lower Cement Concrete Techno-logy (LCCT) is being promoted for reducing OPC content in the concrete by maximum addition of GGBS.
Author :
- Dr. L.R. Manjunatha,
- Vishwanath Kallappa
Visit : www.jswcement.in