Predicting the life of a structure
Prof. A S Khanna, retired from IIT Bombay, chairman SSPC India and is running a Paint Testing Company and also giving consultancy on paint related activities : recommendations of paints for various systems, paint failures, categoraistaion of areas based upon its corrosion level and recommendations of protective coatings.
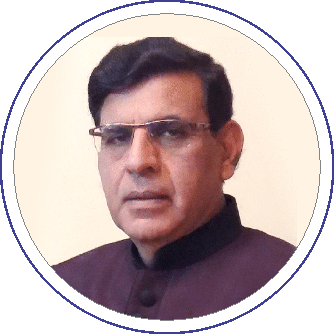
Khanna Paint Testing Laboratory (OPC) Pvt. Ltd
Safety of structure with lowest maintenance is perhaps the most important requirement of a best construction. Further, no plant manager would want any unwanted plant shutdown due to the failure of the plant component, and then spend time for its replacement.
Material selection is the first step once a rough design of the plant is ready. Based on the selection, one can fix the thickness of different components and also the environment, which will help predict the life of the component.
Any chemical or process plant has three main categories of materials:
In the case of materials used for structural application of the plant, more than 80 per cent of this is normal steel. Many of these structural steels usually are exposed to atmospheric environment. Thus, based on whether the environment is from C1-C5 type, corrosion protection can be controlled by a paint coating suitable in that environment. However, additional precautions are needed if the pollution due to the plant is also affecting the structural steels. For structural steels, one either uses galvanised steel or carries out painting after the fabrication. If in the initial stages, the members are properly shotblasted followed by a suitable paint, for example, an epoxy intermediate coat after a Zn based primer coat with a top layer of polyurethane, it will give a life of six to eight years. Use plastics, polyvinyl chloride (PVC)/ corrugated polycarbonate (CPC) or fibre reinforced plastic (FRP) wherever possible in place of metallic materials where aqueous corrosion is an issue. This prevents material degradation to a larger extent.
For the actual plant component, the material requirement can be different and can be based on the environment & temperature needed. It can be a low-alloy steel, stainless steel or a superalloy. For example, for a component exposed to water/steam system, it is always advisable to use ferritic steels or low-alloy steels. Austenitic material should not be exposed to water/steam environment. For seawater circulation or condenser cooling type of applications, either Monel (Ni:Cu in 70:30 ratio) or duplex/ super austenitic/ ferritic stainless steels can be used. For high temperature applications, the choice of the alloy can be made depending on the temperature. It must be known whether the temperature is above 900°C or below. For temperatures below 900°C, chromia based alloys can be used, and for temperature above 900°C, alumina based alloys can be used.
Whether the environment is sulphur free or containing sulphur, also decides the choice of the alloy. An environment with strong sulphur activity must be chosen with high Cr content. Pure oxidation environment can have low-Cr content of an alumina forming alloy. Temperature requirement also needs the selection of material based on its strength requirement at that temperature as well as its creep properties. Standard austenitic stainless are good upto 750°C, and high-alloy stainless steels can go up to 900°C. For temperature above 900°C, it is advisable to use superalloys.
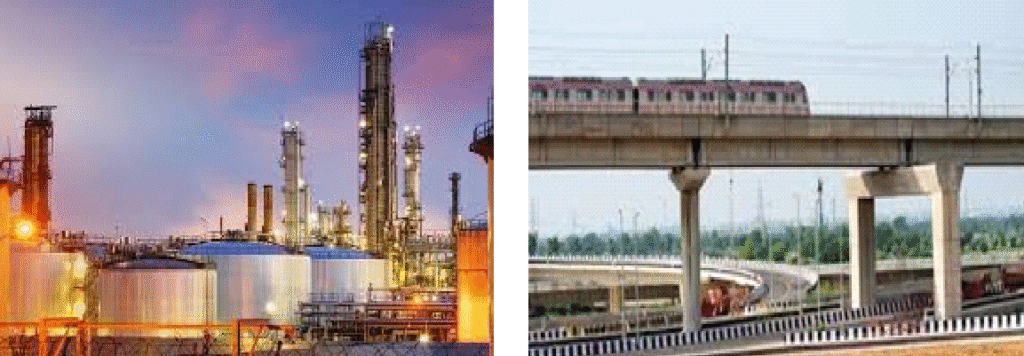
How to decide their life?
Once the materials have been selected, how does one make sure that they will give the expected life or not? Life prediction becomes an important aspect. Generally, it is based on factors such as corrosion allowance, past experience (own or reported), fracture mechanic approach, etc. But, in practice, one finds that there are several questions that need to be answered on such a prediction. For example, fracture mechanics is advocated as the primary mechanism of predicting failures.
However, KIC (fracture toughness test) is usually irrelevant until defects have progressed significantly into the material. The larger problem is preventing the penetration at the outset; predicting and preventing the occurrence of such initial penetrations is primary. Another example is ‘corrosion allowance’ to account for future corrosion damage. Unfortunately, the corrosion allowance does not account for any of the localised corrosion processes and various flow-accelerated corrosion phenomena. Thus, corrosion allowance is misleading. Many a times one predicts corrosion assuming the environment is pure water. This, however, can give wrong prediction as many chemical species present in ppm level in the relatively pure water can concentrate due to heat transfer and boiling on surfaces. Unwarranted reliance on inappropriate accelerated tests has led to some major mistakes in the selection of materials and design, as in many cases, the results of accelerated tests are difficult to be extrapolated due to change in mechanism of corrosion. The difficulty of communication between designers and those who understand predicting performance has often led to lack of serious consideration of potential failures.
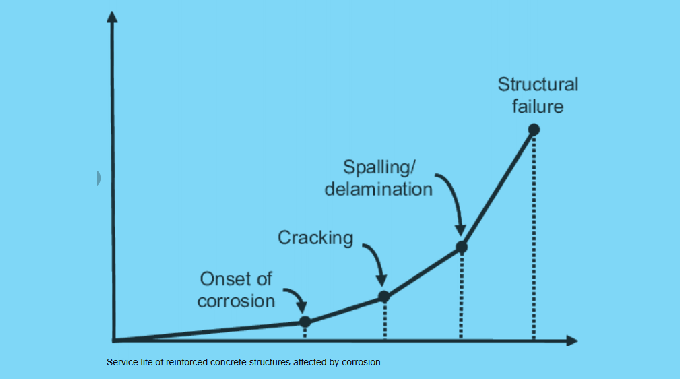
A new approach
To overcome some of these problems, Roger Staehle developed the Corrosion Based Design Approach (CBDA) and the Location for Analysis Matrix (LAM) as means for providing a rigorous approach
to quantify and organise the necessary information for prediction. Many hurdles come in the way while developing an approach of prediction. There are some inherent problems that question life prediction such as continuous change in conditions with time, attack by multiple environments on the same component, occurrence of corrosion by components, which are not considered as part of environment, etc. For example, corrosion of heat exchanger tubes by Cu ions contamination from condenser tubes. Lack of knowledge of field experience and statistical nature of corrosion-related failures are inherent as they involve diverse inputs from the material and environment exhibits ‘broad scatter’. In discussing the dependencies of the steps in the CBDA as well as in the LAM, the term ‘principal variables’ is used. The seven principal variables that affect the modes of corrosion are: temperature, stress, pH, electrochemical potential, concentration of species, alloy composition and alloy structure.
CBDA steps
The following are the ten steps of CBDA:
Environmental definition: ‘Defining the environment’ is the most important step in predicting performance. It is also the step that is given least attention and for which there is little understanding by the technical community. It is important to define the environment from all possible angles, which can cause damage to the material, location and even chronology of the attack to be considered.
Material definition: It is important to define material completely; steel means, low alloy, normalised or tempered, micro alloyed; stainless steel means which type and composition, including the extent of tramp elements impurities, inclusions, etc.
Mode definition: The ‘mode’ of corrosion refers to the morphology and avenues by which materials are corroded or degraded. Even the ‘submode’, which refers to the same mode in the same material in somewhat the same environ-ment involves different dependencies on the principal variables. A good illustration of two sub-modes is the stress corrosion cracking (SCC) that occurs in alkaline and acidic environments; both are of the SCC mode but depend differently on principal variables.
Super-position: It has to be considered whether the variables that describe environments on the surface are atleast to some extent coincident with those that describe the various possible modes of failure. If such coincidence occurs, then the materials, designs or environ-ments may need to be modified before any further steps are taken.
Statistical definition: This is one phenomenon that puzzles many in the case of heat exchanger boiler tube consisting of hundreds of tubes. If one finds a small failure in one of the tubes, it can be said that many materials & environmental parameters look uniform throughout the component. However, some micro mechanisms may be different, such as the local micro-structure of the steel may have some inclusions, or inhomogeneity in compositions, slight variations in the microenvironment, etc. The best way to confirm this factor is not to conclude on the basis of one sample, but atleast three samples.
Accelerated testing: The main objective of the accelerated testing is to estimate when the failure would occur under the conditions of the engineering application. Many of the tests are made accelerated, either by increasing the temperature or by carrying out the tests at higher concentration. Both these factors can give misleading information if the mechanism of failure changes either of these – temperature or concentration. Hence, acceleration must be limited to a stage where there is no change in the mechanism of failure from the actual Prediction: Prediction involves utilising the first seven steps of the CBDA to determine whether the design life objective can be reached. Monitoring and feedback: It is not always practical to produce a perfect prediction. It may not be desirable in some cases. However, it is practical to monitor performance. Such monitoring usually includes a combination of periodic inspections and continuous monitoring. This information is then compared to predictions or with certain limits to assess the approach to failure. Results from monitoring are then fed back to operators and designers to determine whether modifications are necessary. Fix: Based on the results from above, together with comparing these results from the predictions, actions are developed to prevent or minimise the occurrence of serious failures. Such actions may involve any of the following: Y Modify the environment to add inhibitors or to change the corrosivity Y Change the design or materials Y Add monitoring equipment.
Conclusion: