What to expect in the Crushing and Screening Industry over the next decade?
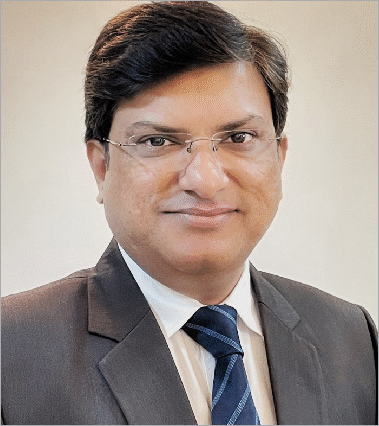
Mineral and Aggregate Crushing Systems
TKIL Industries Pvt Ltd (formerly known as
thyssenkrupp Industries India Pvt Ltd)
Indian Construction & Engineering market is one of the largest in the world. India’s construction industry and mining activities are rapidly growing, leading to an increased demand for crushers, feeders and screeners. Companies are also diversifying their product offerings by introducing advanced and innovative crushers, screeners and feeders in the market. Government plans to monetize assets of worth Billions of dollars in the mining sector over the next decade with the ease of doing business in minerals. Equipment manufacturers are continuously investing in research and development to roll out equipment with advanced technology in order to meet the growing dynamic demand for various end use industries.
Indian Crushing and Screening industry is expected to grow at a healthy growth rate of 7-8%. With the renewed thrust on infrastructure development by the Government of India, the demand for aggregates is bound to increase. The National Infrastructure Pipeline (NIP) includes projects worth INR 109 Trillion* which are under different stages of planning and execution. NIP comprises brownfield and greenfield infrastructure projects of above INR 100 crore across both economic and social infrastructure which will drive the demand for aggregates and M-sand in the coming 10 years.
Changing customers’ expectations
Over the years, the crushing and screening industry has seen many changes in the way of it’s functioning. With the changing business environment and emergence of information techno-logy, the customers are more informed and aware than before. The crushing and screening industry can expect several key trends and developments over the next decade. This has also motivated the Equipment Manufacturers to constantly innovate and make their equipment more reliable and efficient. Customers are no longer looking for the cheapest option. They want reliable and feature rich equipment with best-in-class quality at a reasonable price. Today’s customers are ready to invest in quality and premium equipment as it gives them peace of mind. Quality is a mindset which requires investment in people and processes. Reliability comes from the know-how of engineering and it’s implementation in the products.
Here is what to expect in crushing and screening industry over the next decade.
Technological Advancements
Automation: More equipment will feature automated controls for efficiency and precision. Automation minimizes human intervention in plant operation thereby minimizing breakdowns and downtime. Automation in crushing and screening processes significantly enhances operational efficiency and productivity across the mining and construction industries. By implementing automated systems, operators can control machinery with precision, reducing the need for manual intervention and minimizing human error. Automated crushers and screens can adjust their settings in real time based on material characteristics and production demands, ensuring optimal performance and consistent output. Additionally, automation allows for remote monitoring and operation, which increases safety by reducing on-site personnel exposure to hazardous conditions. Overall, the use of automation streamlines workflows, lowers operational costs, and improves the overall reliability of crushing and screening operations.
AI Integration, Data Analytics and IoT: With the emergence of AI and use of Data analytics for predictive maintenance and optimization of operations, the machines have become smarter than before and will continue to evolve with further technolo-gical advancements. Adoption of IoT technology for real time monitoring and diagnostics is bound to improve efficiency of the equipment thus impro-ving productivity and in turn generating more profits for the customer.
The incorporation of AI, IoT, and data analytics into crushing and screening operations is going to transform the industry by enabling smarter, more efficient processes. IoT sensors collect real-time data on equipment performance, material properties, and environmental conditions, providing a comprehensive view of operations. This data feeds into AI algorithms that analyze patterns and predict potential issues, allowing for proactive maintenance and minimizing downtime. Additionally, data analytics empowers operators to make informed decisions by optimizing settings and workflows based on historical performance and current conditions. Together, these technologies will enhance productivity, reduce costs, and improve safety, creating a more agile and sustainable approach to material
processing.
Hybrid and Electric Solutions:
Hybrid and electric solutions for crushing and screening are gaining traction as the industry shifts towards more sustainable and eco-friendly practices. These innova-tions combine traditional diesel power with electric and battery technologies, resulting in reduced emissions and lower fuel consumption. Hybrid systems offer the flexibility to operate in remote locations without access to a power grid while still delivering the performance required for demanding applications. Electric solutions further minimize the carbon footprint by utilizing renewable energy sources and providing quieter operation, which is especially beneficial in urban environments. As regulations tighten and environmental concerns grow, these hybrid and electric techno-logies not only enhance operational efficiency but also align with the industry’s commitment to sustainability and reduced environmental impact. Industry is witnessing a sustained growth of hybrid and fully electric crushing and screening equipment. The concept of fully electric mobile plants is already gaining momentum and is expected to grow further over the next decade.
Digital Transformation
Remote Monitoring: Telematics in crushing and screening will play a crucial role in optimizing operational efficiency and enhancing equipment management. By integrating GPS and cellular technology, telematics systems provide real-time monitoring of machinery performance, location, and usage patterns. This data allows operators to track equipment health, enabling predictive maintenance and reducing unexpected downtime. Additionally, telematics facilitates more efficient fleet management by providing insights into fuel consumption, load optimization, and operational hours, leading to cost savings and improved productivity. With the ability to remotely access performance metrics, operators can make informed decisions quickly, ensuring that crushing and screening processes run smoothly and effectively while maximizing resource utilization.
Growth in digital and remote monitoring solutions for better management and oversight of operations will drive operational efficiency in the next decade. This is particularly useful for customers having multiple sites. A single dashboard providing information about all the sites can provide the customer with complete peace of mind.
Software Integration: Integration of software solutions for project manage-ment and equipment tracking. More and more features will get integrated into the system which can be managed and operated from remote locations with an integrated control room for multiple sites.
Modular and Mobile Solutions for Emerging markets
There is a rise in demand for modular systems that can be easily transported and adapted to various sites thus providing flexibility to the customer. The trend towards modular crushing and screening machinery is rapidly gaining momentum as industries seek more flexible and efficient solutions. Modular systems are designed for easy assembly, disassembly, and transport, allowing operators to quickly adapt to changing site conditions and production requirements. This versatility enables businesses to optimize their operations by scaling up or down as needed, minimizing downtime and enhancing overall productivity. Additionally, modular designs often incorporate advanced technologies such as automa-tion and IoT connectivity, facilitating seamless integration with existing systems. Urban projects require flexible and scalable crushing solutions thereby increasing the demand for smaller, more efficient machines for urban environ-ments especially in the demolition and recycling space. Compact equipment are particularly favored in urban settings where space is limited, offering efficient solutions for construction challenges. With the increased infrastructure projects in developing countries, there will be a boost in demand for crushing and screening equipment. As sustainability becomes a key focus, crushing and screening systems also tend to have a smaller environmental footprint, making them an attractive choice for companies looking to enhance efficiency while adhering to eco-friendly practices. Overall, the shift towards modular crushing and screening machinery reflects a broader industry movement towards agility, efficiency, and sustainability.
Environmental and Compliance Regulations
Compliance and regulatory challenges in the crushing and screening industry are increasingly complex, driven by stringent environmental standards and safety regulations. Operators must navigate a landscape of laws governing emissions, noise pollution, and dust control to minimize their environmental impact and ensure worker safety. This often requires investing in advanced
technologies and equipment that meet regulatory requirements, such as dust suppression systems and noise-reduction measures. Additionally, companies must stay updated on changing regulations at local, national, and international levels, which can vary significantly and require continuous training and adaptation. Failure to comply can result in hefty fines, legal repercussions, and reputational damage, making it essential for industry stakeholders to prioritize compliance as a core component of their operational strategy. As sustainability becomes a priority, the industry faces the dual challenge of meeting regulatory demands while striving for operational efficiency and profitability.
With the industry’s focus on low carbon footprints, there is a certain growth in the demand for energy-efficient and low-emission machines. With the increased focus on recyclable materials, the demand may increase for mobile and modular systems. Customers have already started looking at ecofriendly and recyclable equipment having minimal environmental impact.
Sustainability
Sustainability in the crushing and screening industry is becoming a fundamental focus as companies strive to minimize their environmental impact and promote responsible resource management. Efforts include the adoption of energy-efficient technolo-gies, such as electric and hybrid machinery, which reduce emissions and lower fuel consumption. Additionally, many operators are implementing advanced dust suppression and waste management practices to mitigate air and soil pollution. The use of recycled materials in crushing processes is also gaining traction, further reducing the demand for virgin resources and promoting circular economy principles. Furthermore, innovations such as modular systems enhance operational flexibility and efficiency, allowing for less energy-intensive setups. As regulatory pressures and public awareness of envi-ronmental issues increase, sustainability initiatives are not only beneficial for the planet but also enhance the long-term viability and competitiveness of companies in the industry.
Some of the key sustainability initiatives are listed below:
Energy Efficiency Improvements
Upgrading Equipment: Modern crushers and screens are designed for higher efficiency, consuming less energy while maximizing output. Investing in energy-efficient machinery can drastically reduce the overall energy consumption of operations.
Use of Renewable Energy: Companies can harness solar or wind power to operate their facilities, significantly decreasing reliance on fossil fuels. Solar panels can be installed on-site to provide a sustainable energy source.
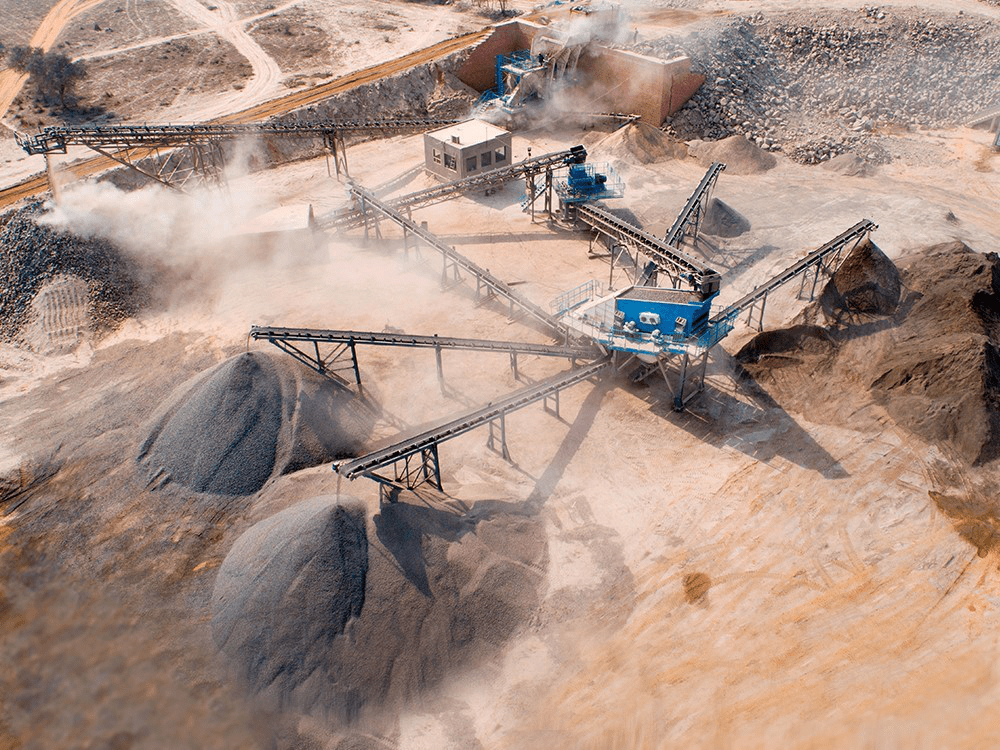
Waste Management and Recycling
Reusing Materials: Implementing strategies for reusing crushed materials within construction projects not only reduces waste but also decreases the demand for new raw materials.
Effective Waste Management:
Establishing a comprehensive waste management plan ensures that materials are recycled whenever possible, minimizing landfill contributions.
Water Conservation Practices
Closed-Loop Water Systems: These systems recycle water used in the washing and processing of materials, reducing overall water consumption and preventing contamination of local water sources.
Rainwater Harvesting: Collecting and using rainwater for operational needs can further reduce dependency on ground-water sources.
Sustainable Supply Chain Management
Local Sourcing: By sourcing materials locally, companies can reduce transpor-tation emissions and support local economies. This approach also minimizes the carbon footprint associated with long-distance transport.
Supplier Collaboration: Partnering with suppliers who share sustainability goals can enhance the overall eco-friendliness of the supply chain.
Technological Innovations
Smart Technology Integration: Utilizing IoT (Internet of Things) devices and AI (Artificial Intelligence) can optimize operations, leading to reduced energy consumption and waste. These technolo-gies can monitor equipment performance and improve maintenance schedules, ultimately extending machinery life.
Carbon Capture Solutions: Emerging technologies for carbon capture and storage can help mitigate emissions during crushing and screening processes, allowing companies to offset their carbon output.
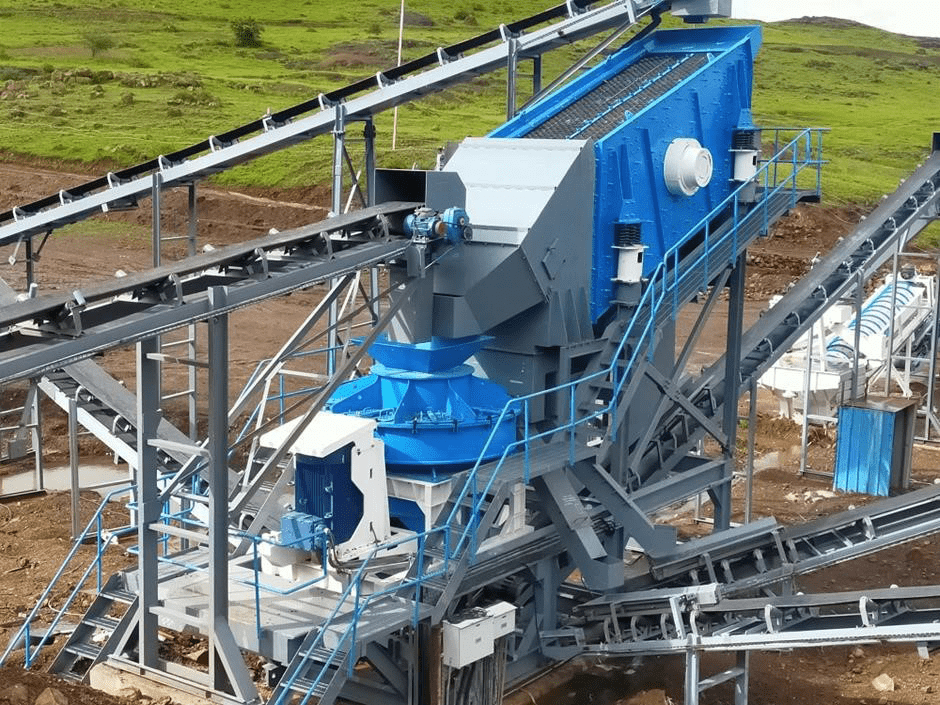
Focus on Safety and Health
Safety and health compliance in the crushing and screening industry is paramount, given the inherently hazardous nature of the operations involved. Over the next decade, companies and mine operators will have to adhere to strict regulations governing workplace safety to protect employees from potential risks such as machinery accidents, noise exposure, and dust inhalation. Implementing comprehen-sive safety training programs, conducting regular equipment inspections, and utilizing personal protective equipment (PPE) are essential strategies for mitigating risks. Additionally, many operators are investing in advanced technologies, such as automation and remote monitoring, to reduce the need for personnel in high-risk areas. Regular audits and risk assessments help ensure compliance with health and safety regulations, fostering a culture of safety that prioritizes the well-being of workers. By maintaining rigorous safety standards, organizations not only comply with legal requirements but also enhance operational efficiency and employee morale, ultimately contributing to a safer working environment.
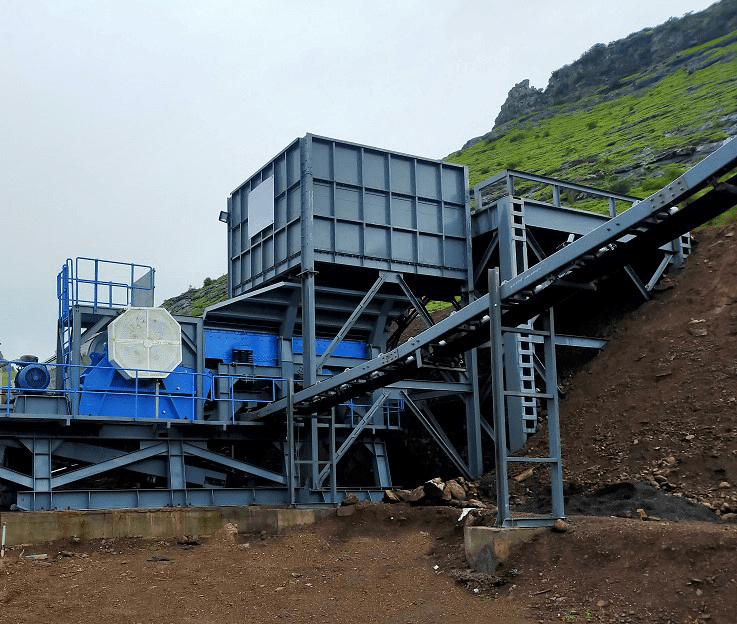
Enhanced Safety Features: More emphasis on equipment that ensures operator safety and health regulations compliance.
Training and Best Practices: The next decade will witness growing importance of workforce training in safe operating procedures. Operator training needs in the crushing and screening industry are critical for ensuring safe, efficient, and effective operations. As machinery becomes increasingly advanced, with the integration of automation and digital technologies, operators must be well-versed in both traditional equipment handling and modern operational techniques. Comprehensive training programs should cover essential topics such as equipment operation, main-tenance procedures, safety protocols, and environmental compliance. Additionally, hands-on training is vital, allowing operators to gain practical experience in real-world settings. Continuous education is also important, as advancements in technology and regulatory requirements evolve. By investing in robust training initiatives, companies can enhance productivity, reduce the risk of accidents, and foster a skilled workforce that is prepared to meet the challenges of the industry. Ultimately, well-trained operators contribute to improved operational efficiency and the overall success of crushing and screening operations.

Conclusion
The future of the crushing and screening industry over the next decade is poised for significant transformation, driven by advancements in technology, sustai-nability initiatives, and evolving market demands. As operators increasingly adopt automation, artificial intelligence, and data analytics, efficiency and produc-tivity will see remarkable improvements, reducing operational costs and enhancing safety. Moreover, the industry’s shift towards eco-friendly practices will prioritize sustainable materials and energy-efficient machinery, aligning with global environmental goals. As infrastructure projects continue to surge and urbanization accelerates, the demand for innovative crushing and screening solutions will only grow. Ultimately, companies that embrace these changes will be well-positioned to thrive in a dynamic landscape, contributing to a more sustainable and technologically advanced future in the construction and mining sectors.
TKIL Industries Pvt. Ltd.
Email : info.macs@tkil.com